Laser welding has become increasingly popular in the automotive industry, offering a range of benefits for vehicle production. From its speed and accuracy to its cost-effectiveness and versatility, laser welding is revolutionizing how cars are built today.
In this article, we’ll explore four ways that laser welding is changing the automotive industry, from improving safety during repairs to allowing manufacturers to create new designs with greater precision. With these advantages in mind, it’s no wonder why so many auto companies have begun to utilize laser welding as part of their vehicle construction process.
Table of Contents
Enhanced Strength and Durability of Automotive Parts
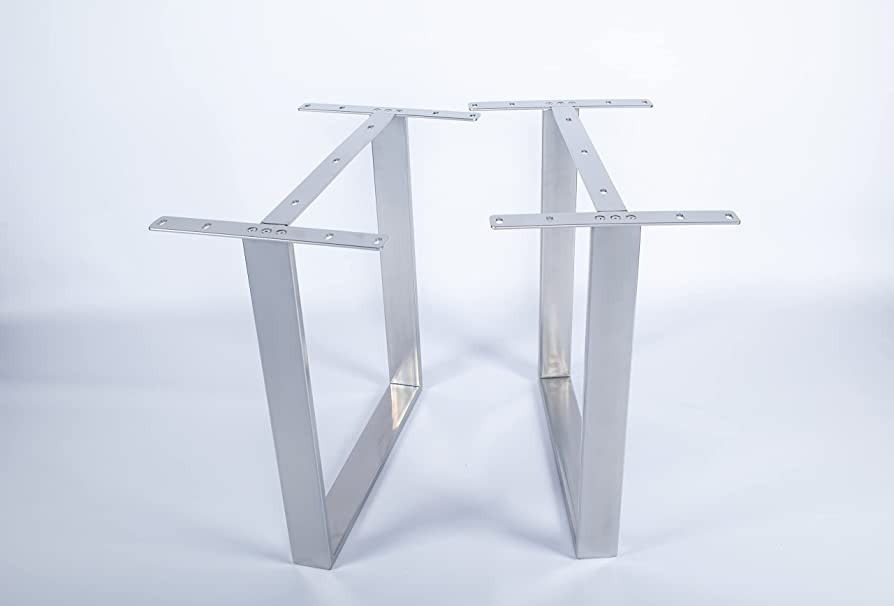
The automotive industry is increasingly turning to laser welding as a viable solution for enhancing the strength and durability of its parts. Laser welding offers several advantages over traditional welding techniques, including increased weld speed, improved joint integrity, and reduced distortion.
It also allows for more complex geometries in parts due to its non-contact nature and high power density. Furthermore, it can provide better fatigue resistance on certain materials compared to conventional methods.
As such, laser welding has become one of the most sought-after processes by automotive manufacturers who are looking for better performance from their products. By leveraging this technology, automakers can produce higher-quality components that are stronger and more durable than those created with traditional methods – leading to a safer driving experience for everyone involved.
Reduced Costs and Improved Efficiency in Assembly Processes
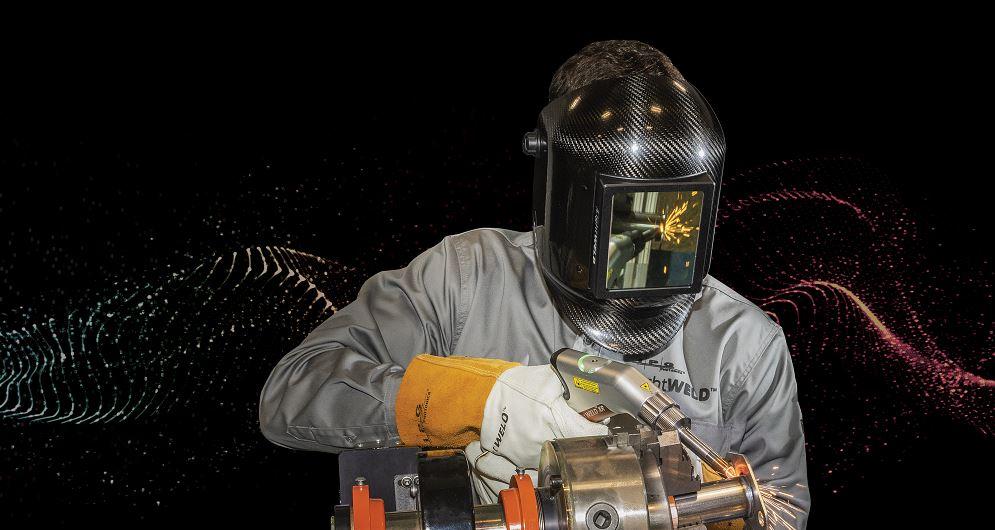
Laser welding has revolutionized the automotive industry, allowing for reduced costs and improved efficiency in assembly processes. One of the key advantages is that laser welding eliminates additional steps needed to secure parts together because it fuses them directly into one piece.
This reduces complexity and cost while speeding up production time as parts don’t need to be transported from one station to the next. In addition, laser welding provides greater precision which helps ensure vehicles are produced safely and quickly without compromising quality.
The accuracy of laser welds also allows manufacturers to reduce waste materials by avoiding over-welding or under-welding spots which can occur with traditional methods such as arc welding. With fewer gaps between components, this increases the durability and performance of vehicles while eliminating potential safety hazards caused by poorly welded pieces.
Laser welding has been a game changer for car makers who rely on precision manufacturing processes, enabling them to produce faster, better quality cars at lower costs than ever before – all thanks to its ability to reduce costs and improve efficiency in assembly processes.
Increased Precision for Complex Joining Applications
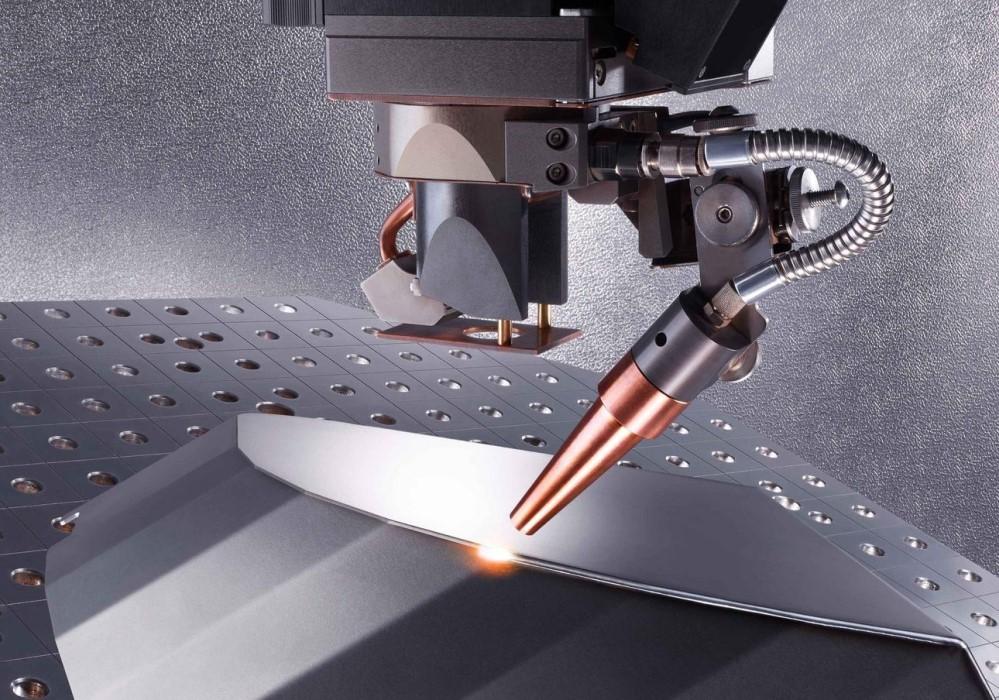
Laser welding has greatly changed the automotive industry by increasing precision for complex joining applications. Its high temperature and speed, as well as its ability to precisely join components with different thermal expansion coefficients, makes it optimal for various types of auto-manufacturing projects.
For instance, laser welding can be used to join steel and aluminum parts to create a lightweight yet strong structure which is essential in most vehicle designs today. In addition, this process allows manufacturers to produce more intricate connections than standard manual welders or robot welders would typically allow.
This increases the accuracy of car assembly lines while reducing costs associated with potential mistakes due to human error or faulty equipment. Laser welding also brings other benefits such as faster production times without sacrificing quality assurance standards that all automotive companies must adhere to.
With laser welding technology at their disposal, auto manufacturers can now build cars with greater precision than ever before – leading to improved performance and safety overall within the industry.
Improved Quality Control Standards in Automotive Manufacturing
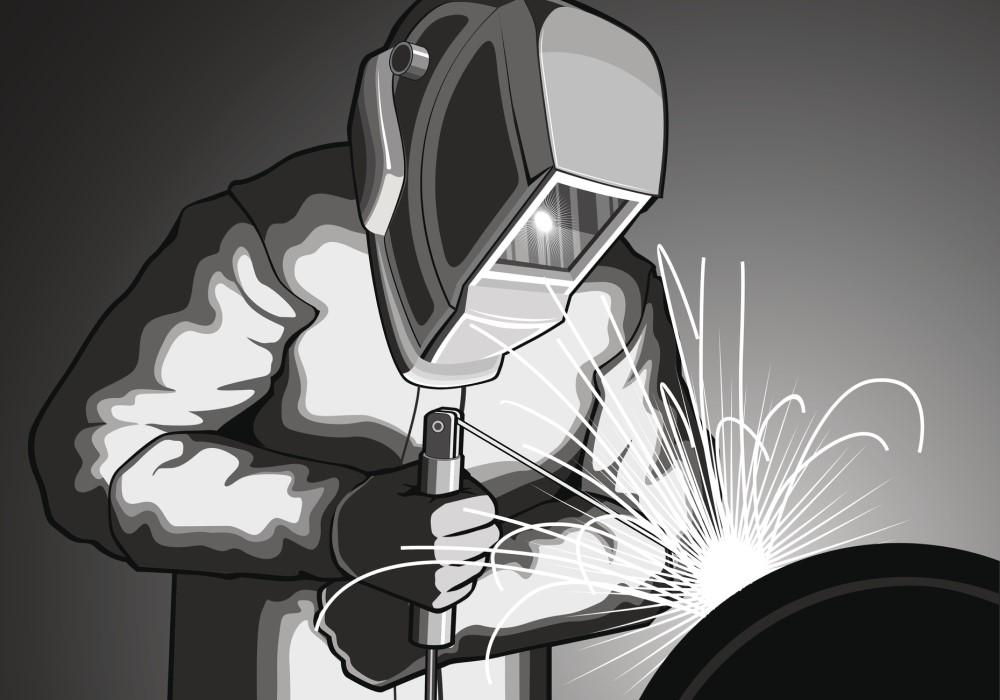
The use of laser welding in the automotive industry has revolutionized the way cars are produced. With improved quality control standards, automotive manufacturers have been able to increase efficiency while producing vehicles with better durability and performance.
Laser welding has enabled car makers to create stronger welds that are more reliable than ever before. This process also reduces costs by eliminating the need for manual labor and improving accuracy in production.
By using advanced technology like lasers, automotive companies can ensure higher quality standards and decrease their overall manufacturing time. As a result, customers can benefit from safer vehicles with fewer defects or malfunctions due to flaws in assembly processes.
In addition, laser welding helps improve energy efficiency during production as it eliminates wasted materials and resources by providing precise measurements when necessary. The improved quality control measures brought about by this technology make sure that only top-notch cars reach consumers’ garages which ultimately leads to greater customer satisfaction levels across the board!
Conclusion
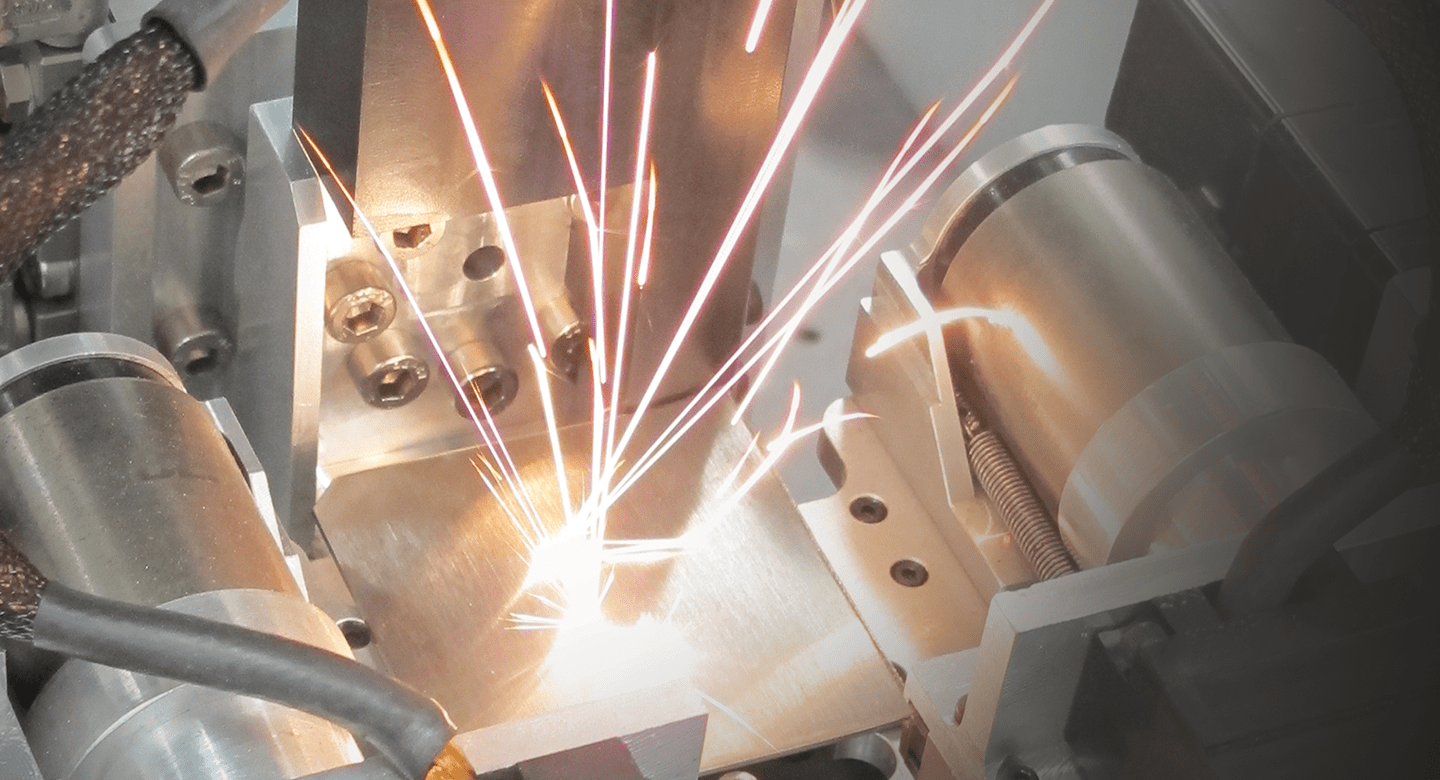
The automotive industry has seen many advancements over the years, and laser welding technology is one of the most innovative and transformative. Laser welding provides a faster, stronger weld with less effort than traditional methods, making it ideal for high-volume production environments.
It also offers greater precision and accuracy in difficult-to-reach areas that cannot be accessed by other methods. The use of a handheld laser welding machine has made this process even more accessible, allowing for shorter cycle times and higher-quality results. With its superior speed and strength, laser welding has revolutionized automotive manufacturing processes around the world.